Smart Palette
Smart Palette was my senior capstone design that was designed by a team of five MEs, including myself. The device is designed to be a consumer product that can extrude a user defined color of paint. The frame was built with 80/20 aluminum and mounted on a stepper-motor-driven Geneva drive to ensure accuracy on location. Then the linear actuator with a touch sensor can push the plunger to dispense the desired amount of paint. The touchscreen UI works with our custom color theory algorithm to calculate the proportion of paint necessary to achieve the user selected color at the requested volume. We also included a color sensor that could scan a color to allow users to create paint colors taken from the world around them.
We presented to a panel of jurors and placed first within our track. Our developed color algorithm had an average of a 96.8% match based on the five set input colors our design had. The actuation dispensing system operated with 94% accuracy after applying our calibration curves to the output model. The design is meant to be a consumer product that can be used in art classrooms or studios to properly teach color theory to beginners or offload arduous ratio matching for experts. Color matching of viscous, non-Newtonian fluids is difficult for any level of artist, so our design would be first to market with such difficult constraints. The fully formatted pdf is available for reading at the bottom of this section.​
​
Design Solution:
​
-
Color Detection and Analysis: A color sensor equipped with an embedded LED was installed into custom 3D-printed housing to standardize each reading and calibrate the sensor against known values. This then read the RGB value of the desired paint, converted to CMYK to analyze in a latent space, then runs a custom algorithm to find the closest possible paint color achieved with the five input paint available. Further in the algorithm, we calculate the correct proportion of each of these paints to dispense to achieve the target color with as much accuracy as possible.
-
Paint Dispensing System: The system uses a rotating carousel and a linear actuator to precisely dispense paint from five base color reservoirs onto a palette. The Geneva drive and stepper motor ensure accurate positioning for the paint extrusion. Increasing the rigidity of the structure was crucial to getting the correct amount of paint dispensed. The structure was both designed and iterated in SolidWorks. Then, the calibrations curves below were found experimentally to predict the error in the system and account for it.
-
Mechanical Components: A linear actuator dispenses paint by extending towards the paint tubes, with a touch sensor for volume control. The carousel subsystem, powered by a Geneva drive and stepper motor, positions paint canisters for accurate color dispensing.
-
Electronic Components and GUI: The EZO-RGB color sensor, paired with a graphical user interface on a touchscreen, enables accurate color detection and user control. This system, designed for compatibility with a Raspberry Pi, adjusts RGB to CMYK for paint mixing based on available base colors. The user is able to interface with a touchscreen to select their colors manually or with the color sensor. Then, the proportions are displayed and the user can choose the volume desired.
​
Design Process:
​
-
Team Formation and Task Allocation: The Smart Palette project combined artistic and scientific disciplines, leading to the formation of two focused groups: mechanical and electrical teams. The mechanical team concentrated on structure and mechanisms, while the electrical team handled power and programming to ensure cohesive operation.
-
Mechanical Design and Prototyping: The mechanical team started with a prototype to validate key features using minimal resources, leading to the development and testing of a dispensing sub-system on an initial prototype. This phase highlighted crucial design adjustments needed for the final product, including resolving issues with actuator alignment, paint tube rigidity, and other mechanical challenges without needing in-depth electrical knowledge.
-
Electrical Design and Sensor Integration: The electrical team, though smaller, chose the RaspberryPi for its versatility in controlling various system components and began with addressing a mismatch in motor wiring that demanded additional controllers. The team's progress included replacing an initially chosen color sensor with the EZO-RGB sensor for its integrated features and better compatibility with system requirements, leading to highly accurate color detection.
-
Algorithm Development and System Calibration: The team focused on converting RGB values to a modified CMYK scale to approximate desired colors using available paints, achieving a high match rate and accuracy through an innovative color algorithm. This process also involved detailed calibration of the color sensor against known color values and adjusting for biases, significantly enhancing the color matching capability of the Smart Palette system.
​
​
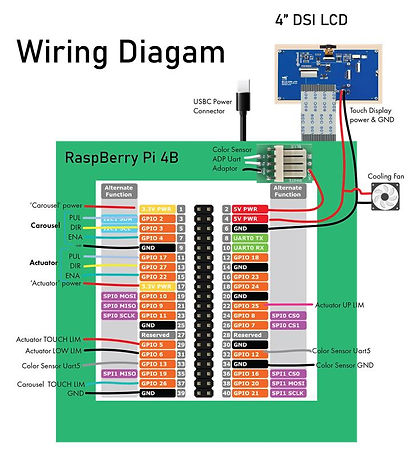
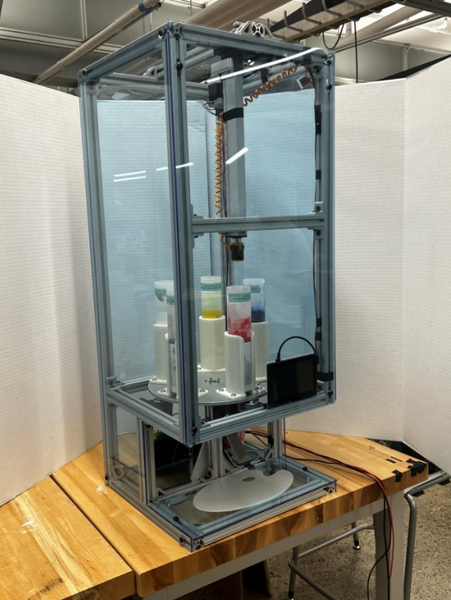
Results:​
​
The success of our final prototype can be defined as a fully functioning electromechanical system, color algorithm, graphical user interface, and rigid frame housing all the components. Our paint dispensing system operated as intended, extruding various amounts of paint based on user input. The dispensing mechanism initially output unreliable values; however, by both increasing the rigidity of the system and developing calibration curves for each paint, the error of the system was mitigated. Though the outputs are still not exact, the uncertainty in the system is not visible in the tangible paint mix. The carousel rotated into the correct position and withstood large loads from the actuator.​
​
Further, the actuator and touch sensor assembly correctly functioned in parallel. The touch sensor reliable denoted when the actuator had contacted the plunger of the paint cannister. From there, the actuator code would successfully execute, driving the actuator into the plunger of the paint tube to dispense the desired amount. The color sensor could successfully read any color without the need to recalibrate before use due to the designed standardized housing. The color achieved a 96.8% average match rate for any possible color, which is within the satisfactory range given the input of only five colors. The GUI was user friendly and provided multiple options to select colors, be that the color sensor or color library. The physical LCD touch screen worked and seamlessly communicated with the rest of the system. The rigid aluminum frame did not deform when loads were applied after sufficient testing and reinforcement. Finally, the acrylic siding added a necessary barrier protecting the sensitive electronic components. All these elements worked together harmoniously to develop a tuned system.

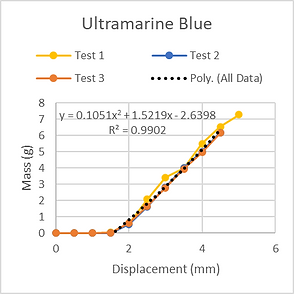

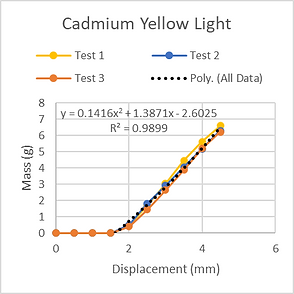
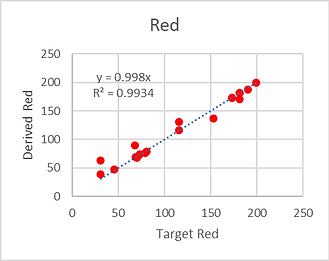
