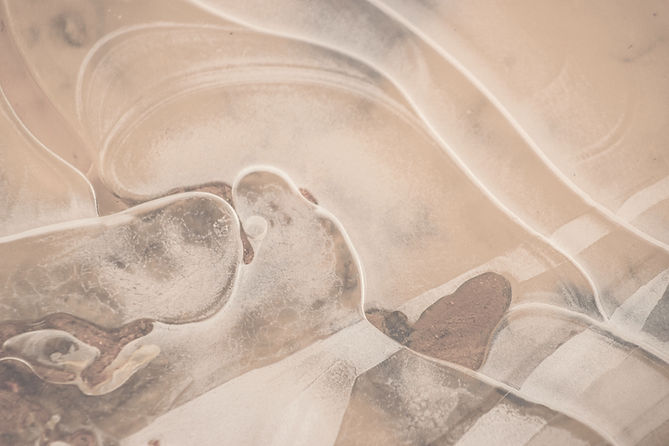
Functioning Model Hand
This was a personal project that I undertook to make a model hand to hold a ball through full remote control. Using band saws, scroll saws, and a mill and lathe, the final product below was achieved. A Lego NXT motorized system used worm gears and further gear trains to optimize the torque and output force of the hand, while also slowing down movement. Two controllers were the paired through Bluetooth to control all fingers except the pinky, which was linked to the ring finger.

Overall Design
The hand was mounted to a wood frame by heat treating a steel bar bend to the desired angle. Then, the steel bar was bolted to the base and the non-dynamic side of the hand. From there, the motor mechanism was externally constructed and placed underneath, with the wires threaded through holes in the base to allow for tension to contract the fingers. A high gear ratio was obtained to create a higher amount of torque, while also allowing the RPMs to drop to a reasonable hand speed. The wire was then threaded around the white wheels below to prevent tangling and frictional errors.
Palm Design
Here the hand can be seen a bit closer. Each metacarpal and phalanges were carved with a groove to have a wire be able to enact a contracting force. Each linkage is trapezoidal to constrict bending motion to only go inward, similar to a human hand. The palm and thumb are also loaded with their own spring system to allow the thumb carpal to fold inward to be able to not only curl fingers, but also grip with the palm.


Spring Loading and Steel Bar
The back of the hand was spring loaded with a spring coefficient that was balanced to not be too difficult to stretch, but also not too low as to not be able to pull the fingers back. Further, the steel beam used and bent can be seen here. The hand does not touch the base anywhere else, so a bending moment analysis and AGMA bolt stress was conducted to see if there would be any failure when the system was under load. It was yielded that the bending moment factor of safety with the expected applied force was n = 12.2 and the screw failure was n = 28.4, so the design was not expected to fail.
Gearbox Design
The gear box can be seen slightly better here. There were 4 motors attached to the Lego NXT, which was coded in the Lego Mindstorm UI using Visual C++. Each motor was spooled around a wheel connected to shaft that ran concentrically through a worm gear, attached to another gear train. There was scope to try to create a universal driveshaft and a series of differential gears, but the parts for that were expensive, so instead, each wheel had it's own drive shaft.
