
RASC-AL NEU - Mars Rover Project
As part of the SEDS (Students for the Exploration and Development of Space) club here at Northeastern, I was tasked with taking the Mechanical Engineering lead on the Mars rover project within the club sponsored by NASA's Jet Propulsion Lab. The project had an exceedingly large scope, but the output that the team produced was very impressive. An initial proposal was required for the first stage of the national competition, where more than 100 other colleges and universities participated. Of them, 12 teams were selected to move on, including the Northeastern team! From there, we presented to a JPL panel of engineers and ended up with the award for "Most Creative Design" and a top 5 finish, which was exciting for all the hard work put into it.
Robot Design
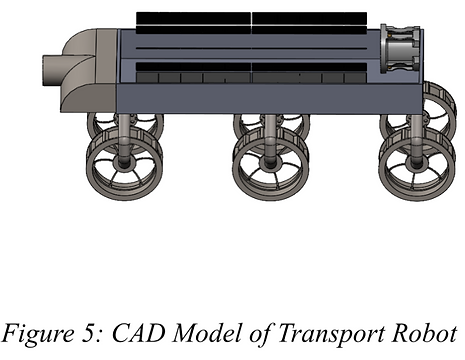
Each Robot is powered by an MMRTG (multi-mission radioisotope thermal generator), similar to the Curiosity or Perseverance rovers, which is capable of generating 120W at 30V over the duration of 5 years. This robot is tasked with transporting both drills and collected propellant water. The tank is capable of storing 75L of water and is initially at Martian atmospheric pressure at which water rapidly evaporates, so the first tank's evaporation is used to pressurize the tank for future trips. The water in the tank is kept liquid by being coil fed around the MMRTG to act as a heatsink, extracting about 100W of the 2kW of thermal waste, keeping the 75L at 5 degrees C. The transfer port for collecting water is connected to a flexible hose with a magnetically charged tip for alignment. The tip is an inverted conical receptacle with a flat cover on top, designed to fit an equivalently shaped conical tip on the Rodriguez wells/CPS to stay covered from dust while traveling.
Simulation Modeling
The wheel design is chosen to maximize pressure on the soil, increasing soil compaction to minimize shearing. The wheel hub is connected to the external wheel by six titanium springs in order to reduce stresses due to sudden impacts with the terrain. The wheel rims around the grousers prevent the robot from slipping sideways on a slope.
The Swarm autonomy is necessary for the robots to avoid obstacles and each other, so when they carry out missions they are able to avoid collisions and possible redundancies. The Swarm uses a version of EKF-SLAM which allows for accurate readings in barren environments. The sensors needed to run EKF-SLAM on the robot are LIDAR, an IMU, and an odometry sensor in the wheels; they are used to process the terrain moved through and for the robot to localize itself within a given map.
The robots use SLAM software to create a map that will identify obstacles in their path. The robots use EKF-SLAM which creates a stochastic map of vector stacking sensors and landmark states. The map builds through sensor estimation of location and confirmation of landmarks. However, in the traditional EKF-SLAM algorithm the computational complexity and uncertainty grow rapidly with the increase of feature points and enlargement of map coverage. To make EKF-SLAM more computationally manageable and accurate for the robots in a barren environment like MARS, the robots are given predefined submaps.
A simulation environment was created to test the mapping on a dummy model rover in a 3D space seen on the right. The path optimization was a success.
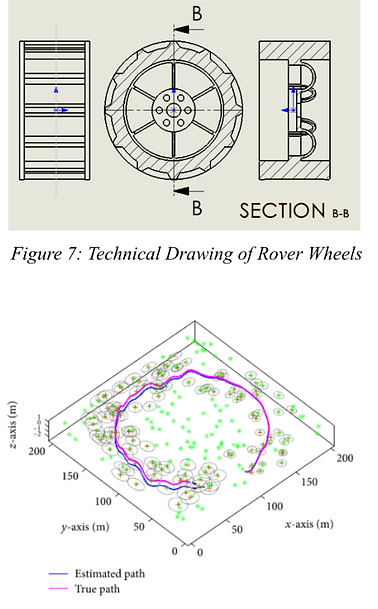
Water Propellant Storage

The storage system will have to store up to 11 T or 6,200 gallons of liquid CH4 and 39 T or 8,200 gallons LOx for 1 year on the Martian surface before the cryogens are removed. The cryogens will need to be stored separately and the cryogenic tanks will need mechanisms to control their internal pressures and temperatures to resist boil-off of cryogen and keep them thermodynamically stable at cryogenic temperature.
A solution to improving packing efficiency would be to use inflatable “bladders” as the basis for the cryogenic tanks so that they could be collapsed in transit to Mars with no dead space.
The optimal origami to use is the Kresling origami structure, due to other research finding it to have maximized compressibility and the minimal number of vertices which allow for points of failure, and for having a simple, one-dimensional deployment process.
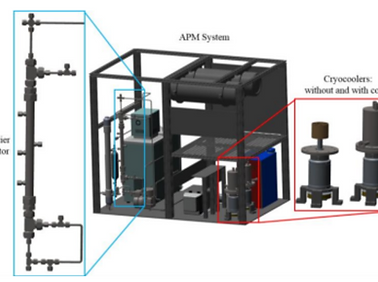